車体を3寸角のバタ材に乗せ、段ボールを敷いて車体の下に潜り、ガードを当ててみる。
このガードは先に試作した方なので思った以上にボルト穴が合わなさそう。4点固定のボルトの内、なぜかタンクのみに固定の1箇所を仮固定して基準にし、穴の位置を油性ペンでマーキングしてゆく。ついでにサスペンション・ダンパーなどと可動部分が接触しそうなところをマーキングして先に削るようにする。
アルミの良い所はその加工性の良さだ。充電ドリルドライバーに穴を広げる為の三角キリという特殊なビットを装着、気持ちが良い程手軽に穴は広がるが、場所によってはワッシャーの外形寸法限度ぎりぎりである。サンダーに研磨用ディスク刃を装着し、取り付け金具の四隅を擦り落としていく。
続いてサンダーに更に細かい研磨用のディスク刃を装着し、アルミ板表面のクリーム色を剥ぎ取ってゆく。こちらも気持ちよく剥がせるので、その落とし穴に気づくのはこの一時間後である。 そう、アルミの地肌を磨いてミラーとまではいかないまでも磨くつもりであった。
しかしディスク刃を換装し、バフと呼ばれる研磨ディスクで磨き始めると、おいらはその間違いにやっと気が付いた。発熱温度が低いため、サンダーでは熱で表面が溶けすぎて磨きにならないのである。ががーん!
後に下請けの板金屋さんに聞くと、一口にアルミと言っても#1000〜5000と種類があり、化合金属や強度により研磨による光沢が可不可な場合もあり、普通製品材以外ではあまり磨かないと言う事でした。また、専門の資材(専用バフや磨き粉)などでしか磨きが出来ない場合もあるとの事、勿論この時点で知る由もありません。廃品とは言え大型電子機器の外装部品だった事を考えれば電解研磨くらいされてたかもしれません。
|
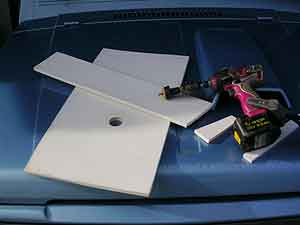
当初、タンクとガードの間に挟む予定だった
ウレタン材。隙間が狭すぎて割愛する。
穴開けに使った充電ドライバー。
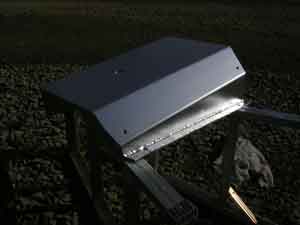
シルバーで塗装をしなおす。写真で見ると
綺麗なんだけれどね〜。
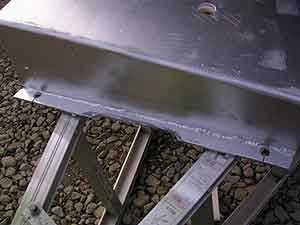
ボルトに溝を作り、応力の逃がしにする。
センターの干渉しそうな部分に切り欠き。
この後もう一回塗装する。
|